- Slate Sealer Stapylton
- Penetrating Slate Sealer Stapylton
- Outdoor Slate Sealer Stapylton
- Non Slip Sealer for Slate Stapylton
- Long Lasting Slate Sealer Stapylton
- Impregnating Slate Sealer Stapylton
- Breathable Slate Sealer Stapylton
- Best Slate Sealer Stapylton
- Sealing Slate Pavers Stapylton
- Sealing Slate around Pool Stapylton
- Sealing Slate Kitchens Stapylton
- Sealing Slate Bathrooms Stapylton
- Sealing Slate Showers Stapylton
- Sealing Slate Benchtops Stapylton
- Protecting against Acid Attack
- Protecting against Salt Attack
- Protecting against Efflorescence
- Why Slate?
- What is Slate?
- What is Efflorescence?
- Maintenance & Care Stapylton
- Slate Stains Removal Stapylton
- Efflorescence Removal Stapylton
- Slate Available Finishes Stapylton
Finishes Available for Slate Stapylton - Gold Coast
While marbles and granites are commonly ground and polished to achieve a high gloss, many types of slatestone in Stapylton are too dense or textured for this treatment. In most cases, slatestone will be honed or finished to a flat or matte appearance. Honed slatestone typically exhibits a smooth, matte surface with minimal sheen.
However, there are several other finishes available for slatestone in Stapylton. Various processes and finishing techniques can yield distinct looks and effects, offering versatility in design and aesthetics.
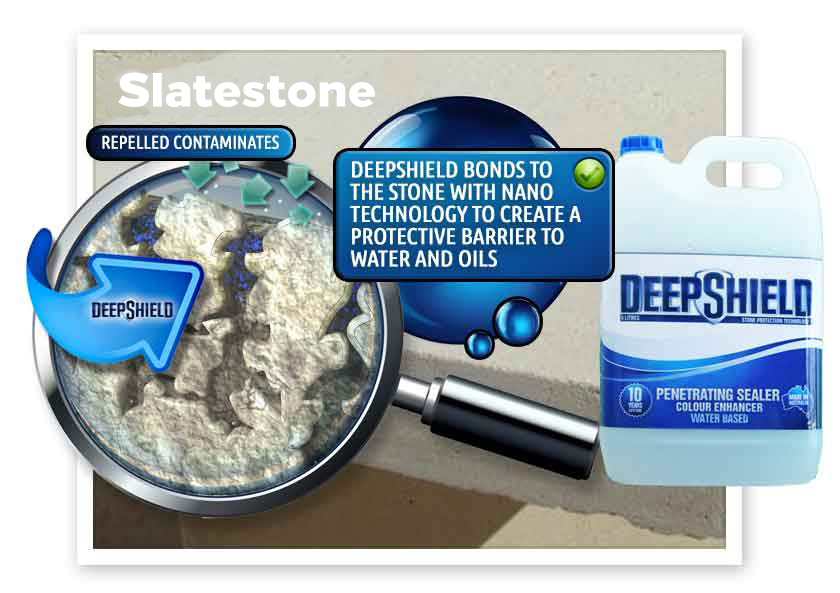
Characterized by a relatively rough surface, the natural slatestone is cut with saws without undergoing additional processes such as honing, tumbling, or flaming. The saw marks are likely to be visible on the surface.
Polished Finish:Characterized by a smooth and reflective surface that enhances the full color and character of the slatestone. This finish is less slip-resistant and typically reserved for indoor areas in Stapylton such as hotel receptions and tabletops. The polishing process involves using increasingly finer abrasives after the honing stage, followed by buffing the stone to achieve a high gloss.
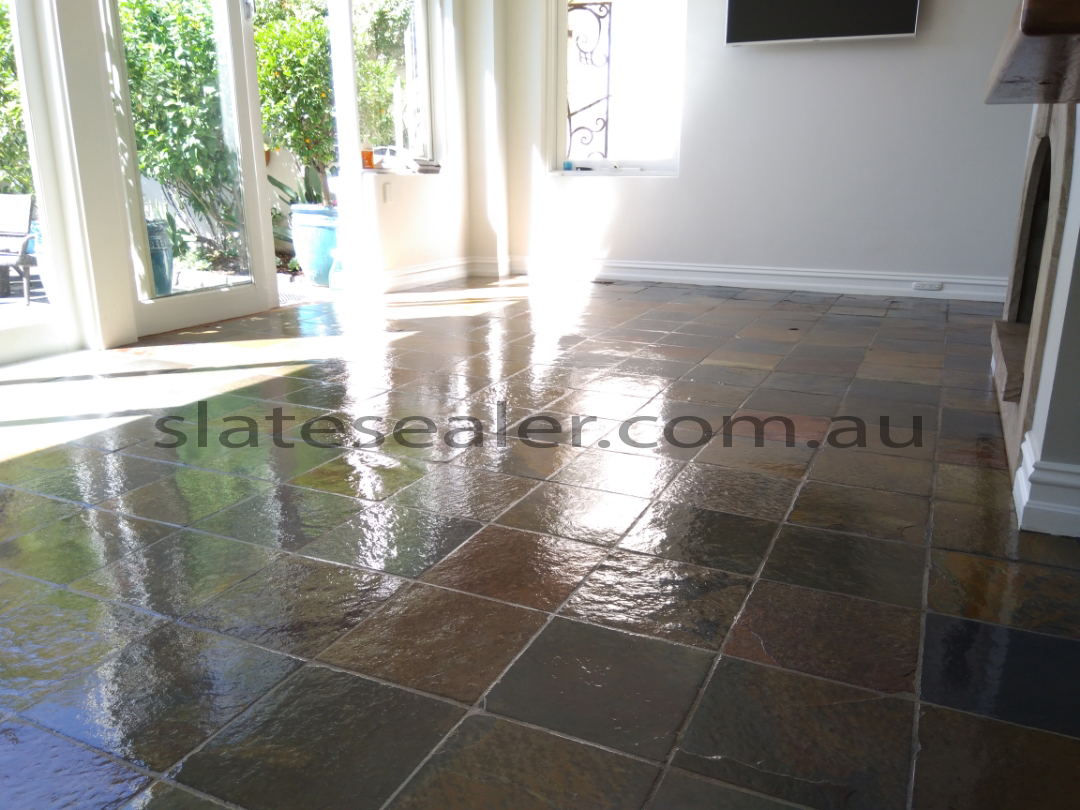
Antiqued/Tumbled Finish:
Tumbling is a common technique used to distress the edges and surface of slatestone in Stapylton by vibrating it in a bath of sand, grit, and sometimes acid. This process results in a finish that appears aged and worn.
Honed Finish:Honing is a less aggressive method compared to grinding, involving the use of coarse grit abrasives to grind and sand the slatestone in Stapylton, creating a smooth but satin, non-reflective surface.
Ground Finish:Ground finishing is a highly aggressive approach to refinishing slatestone in Stapylton, utilizing a heavy-weighted floor buffer with metal-bonded diamond grit to remove deep scratches and lippage. The aim is to flatten the surface and smooth out imperfections, often followed by honing and polishing.
Brushed Finish:Brushing with steel or hard nylon brushes, along with water, is used to wear out softer parts of the slatestone, creating a textured finish that imparts an antique appearance.
Sandblasted Finish:High-pressure sandblasting or shot-blasting creates a textured surface on slatestone in Stapylton. This process can lighten the stone and mask its natural character by obscuring veins and fossils within the stone.
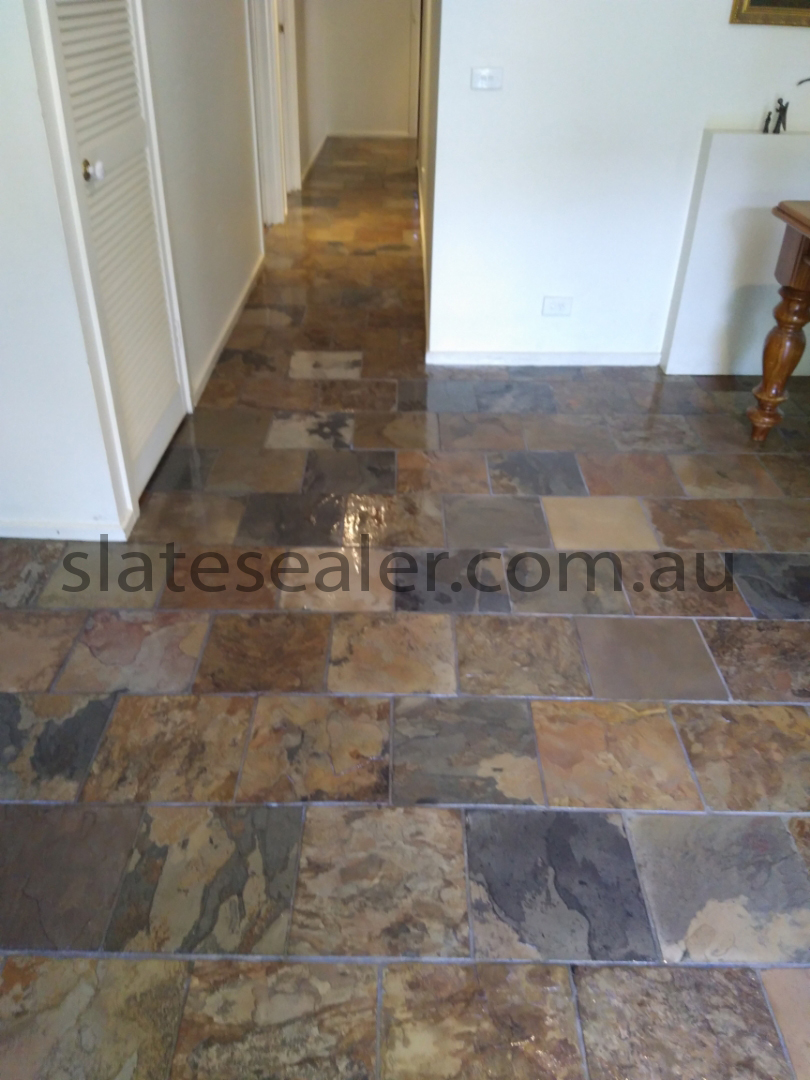
Bush-Hammered Finish:
This technique involves using a bush hammer, either by machine or hand, to impact the surface of slatestone and create a highly anti-slip finish. The result is a textured surface with pitted indentations, providing enhanced traction.
Chiselled Finish:Mechanical chiselling is employed to create lines or grooves in the slatestone, producing an anti-slip finish.
StoneMaster possesses the expertise and capability to resurface slatestone, eliminating scratches and etches to achieve the desired appearance. In most cases of normal wear on natural stone, a simple polish can restore the sheen.In most situations with normal wear on natural stone, a simple polish will restore the sheen.
In cases with heavy wear and etches, StoneMaster can resurface the area and remove all scratches and etches and then polish with a polishing compound to restore the original finish.
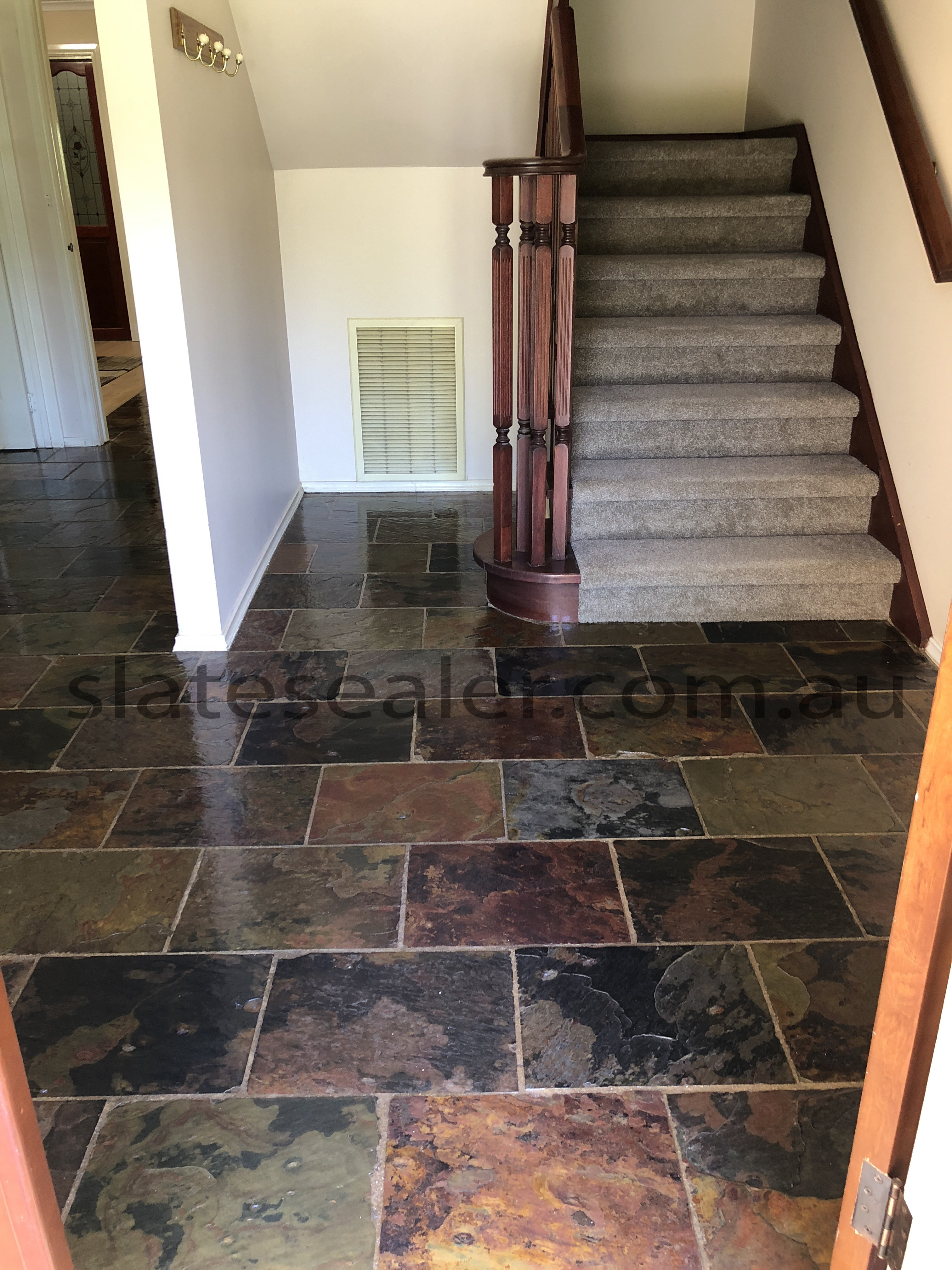
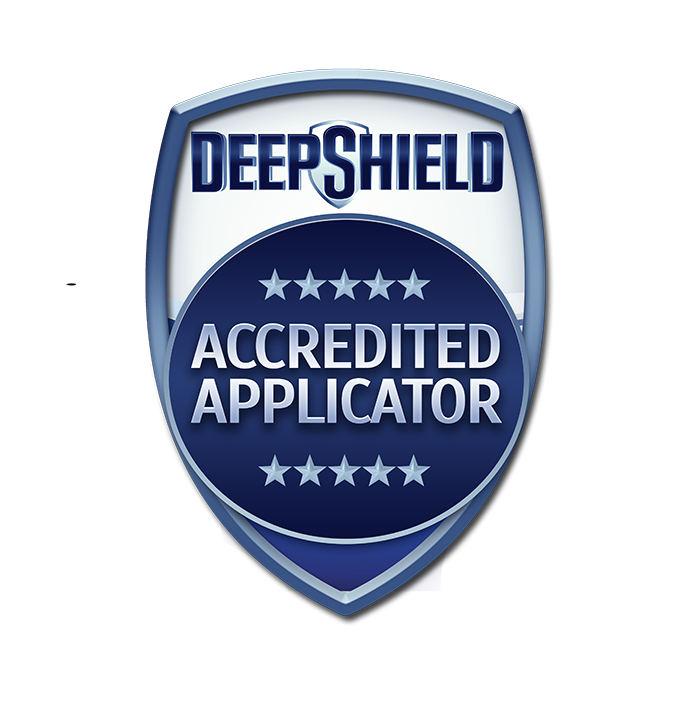